ធន់នឹងទឹកមិនល្អ ផ្ទៃមិនស្មើគ្នា មាតិកាម្សៅខ្ពស់ និងប្រវែងមិនស្មើគ្នា?បញ្ហាទូទៅ និងវិធានការកែលម្អក្នុងផលិតកម្មចំណីសត្វ
នៅក្នុងការផលិតចំណីក្នុងទឹកប្រចាំថ្ងៃរបស់យើង យើងបានជួបប្រទះបញ្ហាមួយចំនួនពីទិដ្ឋភាពផ្សេងៗ។នេះគឺជាឧទាហរណ៍មួយចំនួនដើម្បីពិភាក្សាជាមួយអ្នករាល់គ្នា ដូចតទៅ៖
១. រូបមន្ត
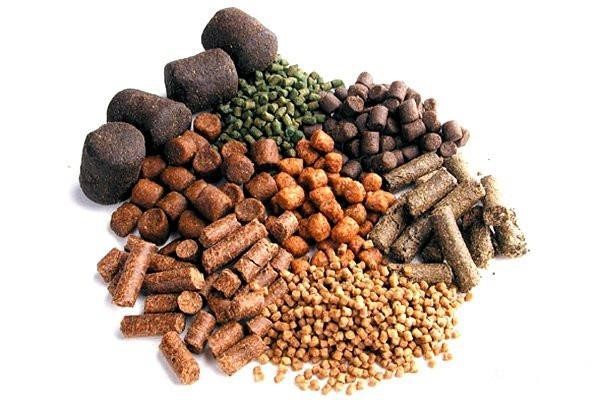
1. នៅក្នុងរចនាសម្ព័ន្ធរូបមន្តនៃចំណីត្រី មានវត្ថុធាតុដើមអាហារច្រើនប្រភេទ ដូចជា អាហារ rapeseed អាហារកប្បាសជាដើម ដែលជារបស់ជាតិសរសៃឆៅ។រោងចក្រប្រេងខ្លះមានបច្ចេកវិទ្យាទំនើប ហើយប្រេងត្រូវបានចៀនជាមូលដ្ឋានស្ងួតដោយមានមាតិកាតិចតួចបំផុត។ជាងនេះទៅទៀត ប្រភេទវត្ថុធាតុដើមទាំងនេះមិនងាយស្រូបចូលក្នុងការផលិតទេ ដែលវាមានផលប៉ះពាល់ច្រើនដល់ការកិនគ្រាប់។លើសពីនេះទៀតអាហារកប្បាសគឺពិបាកក្នុងការកំទេចដែលប៉ះពាល់ដល់ប្រសិទ្ធភាព។
2. ដំណោះស្រាយ៖ ការប្រើប្រាស់នំ rapeseed ត្រូវបានកើនឡើង ហើយគ្រឿងផ្សំក្នុងស្រុកដែលមានគុណភាពខ្ពស់ដូចជាកន្ទក់ត្រូវបានបន្ថែមទៅក្នុងរូបមន្ត។លើសពីនេះទៀតស្រូវសាលីដែលមានប្រហែល 5-8% នៃរូបមន្តត្រូវបានបន្ថែម។តាមរយៈការកែតម្រូវ ឥទ្ធិពល granulation ក្នុងឆ្នាំ 2009 គឺល្អណាស់ ហើយទិន្នផលក្នុងមួយតោនក៏កើនឡើងផងដែរ។ភាគល្អិត 2.5 មីលីម៉ែត្រមានចន្លោះពី 8-9 តោនកើនឡើងជិត 2 តោនបើប្រៀបធៀបទៅនឹងអតីតកាល។រូបរាងនៃភាគល្អិតក៏មានភាពប្រសើរឡើងគួរឱ្យកត់សម្គាល់ផងដែរ។
លើសពីនេះ ដើម្បីបង្កើនប្រសិទ្ធភាពនៃការកំទេចអាហារគ្រាប់កប្បាស យើងលាយម្សៅគ្រាប់កប្បាស និងគ្រាប់ធញ្ញជាតិក្នុងសមាមាត្រ 2: 1 មុនពេលកំទេច។បន្ទាប់ពីការកែលម្អ ល្បឿននៃការកំទេចគឺមានលក្ខណៈជាមូលដ្ឋានជាមួយនឹងល្បឿននៃការកំទេចអាហារ rapeseed ។
២. ផ្ទៃមិនស្មើគ្នានៃភាគល្អិត
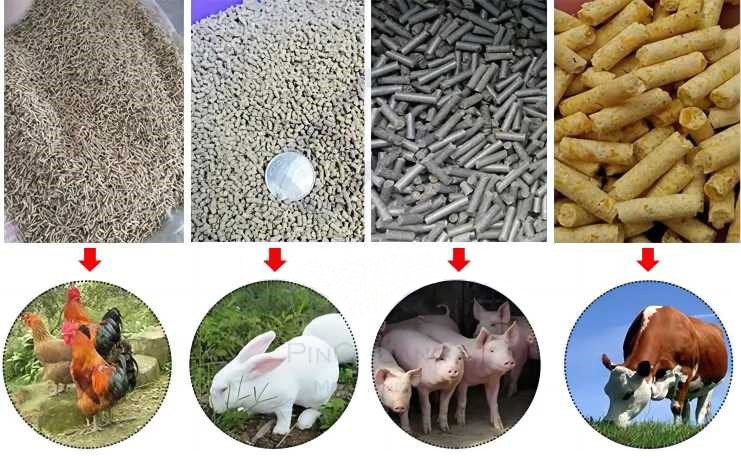
1. វាមានឥទ្ធិពលយ៉ាងខ្លាំងទៅលើរូបរាងនៃផលិតផលដែលបានបញ្ចប់ហើយនៅពេលដែលបន្ថែមទៅក្នុងទឹកវាងាយនឹងដួលរលំហើយមានអត្រាប្រើប្រាស់ទាប។មូលហេតុចម្បងគឺ៖
(1) វត្ថុធាតុដើមត្រូវបានកំទេចខ្លាំងពេក ហើយកំឡុងពេលដំណើរការកំដៅ វាមិនមានភាពចាស់ទុំពេញលេញ និងទន់ ហើយមិនអាចរួមបញ្ចូលគ្នាបានល្អជាមួយវត្ថុធាតុដើមផ្សេងទៀតនៅពេលឆ្លងកាត់រន្ធផ្សិត។
(2) នៅក្នុងរូបមន្តចំណីត្រីជាមួយនឹងមាតិកាខ្ពស់នៃជាតិសរសៃឆៅ ដោយសារតែវត្តមាននៃពពុះចំហាយនៅក្នុងវត្ថុធាតុដើមកំឡុងពេលដំណើរការកំដៅ ពពុះទាំងនេះប្រេះដោយសារតែភាពខុសគ្នានៃសម្ពាធរវាងខាងក្នុង និងខាងក្រៅផ្សិតកំឡុងពេលបង្ហាប់ភាគល្អិត។ បណ្តាលឱ្យផ្ទៃមិនស្មើគ្នានៃភាគល្អិត។
2. វិធានការដោះស្រាយ៖
(1) គ្រប់គ្រងដំណើរការកំទេចឱ្យបានត្រឹមត្រូវ
នាពេលបច្ចុប្បន្ន នៅពេលផលិតចំណីត្រី ក្រុមហ៊ុនរបស់យើងប្រើប្រាស់ម្សៅមីក្រូ 1.2mm ជាវត្ថុធាតុដើម។យើងគ្រប់គ្រងភាពញឹកញាប់នៃការប្រើប្រាស់ Sieve និងកម្រិតនៃការពាក់ញញួរ ដើម្បីធានាបាននូវភាពល្អិតល្អន់នៃការកំទេច។
(2) គ្រប់គ្រងសម្ពាធចំហាយទឹក។
យោងតាមរូបមន្ត លៃតម្រូវសម្ពាធចំហាយទឹកឱ្យសមហេតុផលក្នុងអំឡុងពេលផលិត ជាទូទៅគ្រប់គ្រងជុំវិញ 0.2 ។ដោយសារបរិមាណដ៏ច្រើននៃវត្ថុធាតុដើមសរសៃក្រៀមក្នុងរូបមន្តចំណីត្រី ការស្ទីមដែលមានគុណភាពខ្ពស់ និងរយៈពេលកំដៅសមរម្យត្រូវបានទាមទារ។
៣. ភាពធន់នឹងទឹកខ្សោយនៃភាគល្អិត
1. ប្រភេទនៃបញ្ហានេះគឺជារឿងធម្មតាបំផុតនៅក្នុងផលិតកម្មប្រចាំថ្ងៃរបស់យើង ជាទូទៅទាក់ទងទៅនឹងកត្តាដូចខាងក្រោម:
(1) រយៈពេលខ្លី និងសីតុណ្ហភាពទាបនាំឱ្យមានសីតុណ្ហភាពមិនស្មើគ្នា ឬមិនគ្រប់គ្រាន់ កម្រិតទុំទាប និងសំណើមមិនគ្រប់គ្រាន់ ។
(2) សម្ភារៈ adhesive មិនគ្រប់គ្រាន់ដូចជាម្សៅ។
(3) សមាមាត្របង្ហាប់នៃផ្សិតចិញ្ចៀនគឺទាបពេក។
(4) មាតិកាប្រេង និងសមាមាត្រនៃវត្ថុធាតុដើមដែលមានជាតិសរសៃឆៅនៅក្នុងរូបមន្តគឺខ្ពស់ពេក។
(5) កត្តាទំហំភាគល្អិតកំទេច។
2. វិធានការដោះស្រាយ៖
(1) ធ្វើអោយប្រសើរឡើងនូវគុណភាពចំហាយទឹក លៃតម្រូវមុំ blade នៃនិយតករ ពង្រីកពេលវេលា tempering និងបង្កើនសំណើមនៃវត្ថុធាតុដើមឱ្យបានត្រឹមត្រូវ។
(2) កែសម្រួលរូបមន្ត បង្កើនវត្ថុធាតុដើមម្សៅឱ្យសមស្រប និងកាត់បន្ថយសមាមាត្រនៃវត្ថុធាតុដើមដែលមានជាតិខ្លាញ់ និងជាតិសរសៃឆៅ។
(3) បន្ថែមសារធាតុស្អិតប្រសិនបើចាំបាច់។(សូដ្យូម bentonite slurry ដែលមានមូលដ្ឋានលើ)
(4) ធ្វើឱ្យប្រសើរឡើងនូវសមាមាត្របង្ហាប់នៃចិញ្ចៀនស្លាប់
(5) គ្រប់គ្រងភាពល្អិតល្អន់នៃកំទេចល្អ។
៤. មាតិកាម្សៅច្រើនពេកនៅក្នុងភាគល្អិត
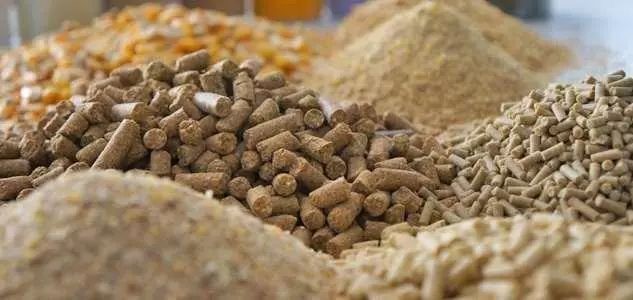
1. វាមានការលំបាកក្នុងការធានានូវរូបរាងនៃចំណីទូទៅបន្ទាប់ពីត្រជាក់ និងមុនពេលបញ្ចាំង។អតិថិជនបានរាយការណ៍ថាមានផេះ និងម្សៅល្អិតៗច្រើនទៀតនៅក្នុងគ្រាប់។ផ្អែកលើការវិភាគខាងលើ ខ្ញុំគិតថាមានហេតុផលជាច្រើនសម្រាប់បញ្ហានេះ៖
ក. ផ្ទៃភាគល្អិតមិនរលោង ស្នាមវះមិនស្អាត ហើយភាគល្អិតរលុង និងងាយនឹងផលិតម្សៅ។
ខ. ការពិនិត្យមិនពេញលេញដោយអេក្រង់ដាក់ចំណាត់ថ្នាក់ សំណាញ់អេក្រង់ស្ទះ ការពាក់បាល់កៅស៊ូធ្ងន់ធ្ងរ ជំរៅសំណាញ់អេក្រង់មិនស៊ីគ្នា ។ល។
គ-មានសំណល់ផេះល្អិតច្រើននៅក្នុងឃ្លាំងផលិតផលសម្រេច ហើយការបោសសំអាតមិនហ្មត់ចត់។
ឃ. មានគ្រោះថ្នាក់លាក់កំបាំងក្នុងការដកធូលីកំឡុងពេលវេចខ្ចប់ និងថ្លឹង។
វិធានការដោះស្រាយ៖
ក. បង្កើនប្រសិទ្ធភាពរចនាសម្ព័ន្ធរូបមន្ត ជ្រើសរើសចិញ្ចៀនស្លាប់ដោយសមហេតុផល និងគ្រប់គ្រងសមាមាត្របង្ហាប់ឱ្យបានល្អ។
ខ. កំឡុងពេលដំណើរការ granulation គ្រប់គ្រងពេលវេលា tempering បរិមាណនៃការផ្តល់អាហារ និងសីតុណ្ហភាព granulation ដើម្បីទុំពេញលេញ និងធ្វើឱ្យវត្ថុធាតុដើមទន់។
គ. ត្រូវប្រាកដថាផ្នែកឆ្លងកាត់ភាគល្អិតស្អាត ហើយប្រើកាំបិតកាត់ទន់ធ្វើពីបន្ទះដែក។
ឃ. កែតម្រូវ និងរក្សាអេក្រង់ចំណាត់ថ្នាក់ ហើយប្រើការកំណត់រចនាសម្ព័ន្ធអេក្រង់សមហេតុផល។
E. ការប្រើប្រាស់បច្ចេកវិជ្ជាពិនិត្យបន្ទាប់បន្សំនៅក្រោមឃ្លាំងផលិតផលសម្រេចអាចកាត់បន្ថយបរិមាណម្សៅបានយ៉ាងច្រើន។
F. វាចាំបាច់ក្នុងការសម្អាតឃ្លាំងនិងសៀគ្វីផលិតផលដែលបានបញ្ចប់ក្នុងលក្ខណៈទាន់ពេលវេលា។លើសពីនេះទៀតវាចាំបាច់ក្នុងការធ្វើឱ្យប្រសើរឡើងនូវការវេចខ្ចប់និងឧបករណ៍ដកធូលី។វាជាការល្អបំផុតក្នុងការប្រើសម្ពាធអវិជ្ជមានសម្រាប់ការដកធូលីចេញ ដែលជាជម្រើសដ៏ល្អជាង។ជាពិសេសក្នុងអំឡុងពេលដំណើរការវេចខ្ចប់ កម្មករវេចខ្ចប់គួរតែគោះ និងសម្អាតធូលីជាប្រចាំ ពីធុងទ្រនាប់នៃមាត្រដ្ឋានវេចខ្ចប់។.
៥. ប្រវែងភាគល្អិតប្រែប្រួល
1. នៅក្នុងការផលិតប្រចាំថ្ងៃ យើងតែងតែជួបប្រទះនឹងការលំបាកក្នុងការគ្រប់គ្រង ជាពិសេសសម្រាប់ម៉ូដែលខាងលើ 420។ ហេតុផលសម្រាប់រឿងនេះត្រូវបានសង្ខេបដូចខាងក្រោម៖
(1) បរិមាណចំណីសម្រាប់ granulation គឺមិនស្មើគ្នា ហើយឥទ្ធិពល tempering ប្រែប្រួលយ៉ាងខ្លាំង។
(2) គម្លាតមិនស៊ីសង្វាក់គ្នារវាង rollers ផ្សិតឬការពាក់ធ្ងន់ធ្ងរនៃផ្សិតចិញ្ចៀននិង rollers សម្ពាធ។
(3) នៅតាមបណ្តោយទិសអ័ក្សនៃផ្សិតសង្វៀន ល្បឿនបញ្ចេញនៅចុងទាំងពីរគឺទាបជាងនៅកណ្តាល។
(4) រន្ធកាត់បន្ថយសម្ពាធនៃផ្សិតចិញ្ចៀនមានទំហំធំពេក ហើយអត្រាបើកគឺខ្ពស់ពេក។
(5) ទីតាំងនិងមុំនៃកាំបិតកាត់គឺមិនសមហេតុផល។
(6) សីតុណ្ហភាព Granulation ។
(7) ប្រភេទនិងកម្ពស់ប្រសិទ្ធភាព (ទទឹង blade ទទឹង) នៃ ring die cut blade មានផលប៉ះពាល់។
(8) ក្នុងពេលជាមួយគ្នានេះ ការចែកចាយវត្ថុធាតុដើមនៅខាងក្នុងអង្គជំនុំជម្រះបង្ហាប់គឺមិនស្មើគ្នា។
2. គុណភាពនៃចំណី និងគ្រាប់ត្រូវបានវិភាគជាទូទៅដោយផ្អែកលើគុណភាពខាងក្នុង និងខាងក្រៅរបស់វា។ក្នុងនាមជាប្រព័ន្ធផលិតកម្ម យើងកាន់តែបង្ហាញឱ្យឃើញនូវអ្វីដែលទាក់ទងនឹងគុណភាពខាងក្រៅនៃគ្រាប់ចំណី។តាមទស្សនៈផលិតកម្ម កត្តាដែលជះឥទ្ធិពលដល់គុណភាពនៃគ្រាប់ចំណីក្នុងទឹកអាចសង្ខេបបានដូចខាងក្រោម៖
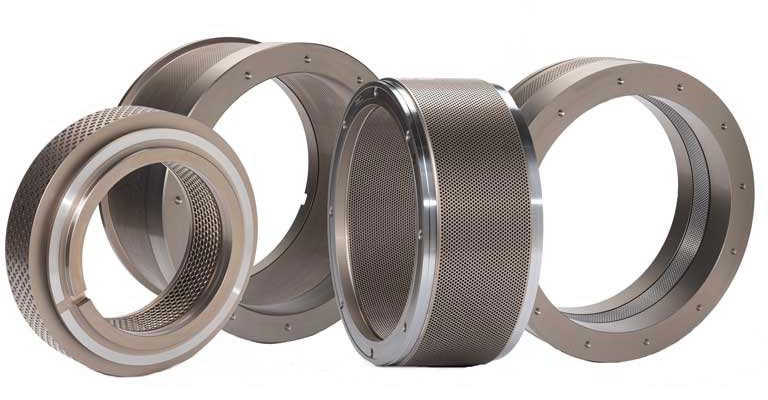
(1) ការរចនា និងការរៀបចំរូបមន្តមានផលប៉ះពាល់ដោយផ្ទាល់ទៅលើគុណភាពនៃគ្រាប់ចំណីក្នុងទឹក ដែលស្មើនឹងប្រមាណ 40% នៃចំនួនសរុប។
(2) អាំងតង់ស៊ីតេនៃការកំទេចនិងឯកសណ្ឋាននៃទំហំភាគល្អិត;
(3) អង្កត់ផ្ចិត សមាមាត្របង្ហាប់ និងល្បឿនលីនេអ៊ែរនៃផ្សិតសង្វៀនមានផលប៉ះពាល់លើប្រវែង និងអង្កត់ផ្ចិតនៃភាគល្អិត។
(4) សមាមាត្របង្ហាប់ ល្បឿនលីនេអ៊ែរ ឥទ្ធិពលពន្លត់ និងសីតុណ្ហភាពនៃផ្សិតសង្វៀន និងឥទ្ធិពលនៃកាំបិតកាត់លើប្រវែងនៃភាគល្អិត។
(5) មាតិកាសំណើមនៃវត្ថុធាតុដើម ឥទ្ធិពលកំដៅ ភាពត្រជាក់ និងការស្ងួតមានផលប៉ះពាល់លើមាតិកាសំណើម និងរូបរាងនៃផលិតផលសម្រេច។
(6) គ្រឿងបរិក្ខារដោយខ្លួនវា កត្តាដំណើរការ និងការពន្លត់ និងកំដៅមានផលប៉ះពាល់លើមាតិកាម្សៅ។
3. វិធានការដោះស្រាយ៖
(1) លៃតម្រូវប្រវែង ទទឹង និងមុំរបស់ឧបករណ៍អេតចាយក្រណាត់ ហើយជំនួសឧបករណ៍អេតចាយដែលពាក់។
(2) យកចិត្តទុកដាក់លើការកែតម្រូវទីតាំងរបស់កាំបិតឱ្យទាន់ពេលវេលានៅដើម និងជិតចុងបញ្ចប់នៃការផលិត ដោយសារបរិមាណចំណីតិចតួច។
(3) ក្នុងកំឡុងដំណើរការផលិត ធានាបាននូវអត្រាការចិញ្ចឹមមានស្ថេរភាព និងការផ្គត់ផ្គង់ចំហាយទឹក។ប្រសិនបើសម្ពាធចំហាយទាប ហើយសីតុណ្ហភាពមិនអាចកើនឡើង វាគួរតែត្រូវបានកែតម្រូវ ឬបញ្ឈប់ទាន់ពេលវេលា។
(4) លៃតម្រូវគម្លាតរវាងសែល roller.អនុវត្តតាមផ្សិតថ្មីដោយប្រើ rollers ថ្មី ហើយជួសជុលផ្ទៃមិនស្មើគ្នានៃ roller សម្ពាធ និងផ្សិតចិញ្ចៀនដោយសារតែការពាក់។
(5) ជួសជុលរន្ធមគ្គុទ្ទេសក៍នៃផ្សិតសង្វៀន ហើយសម្អាតរន្ធផ្សិតដែលស្ទះភ្លាមៗ។
(6) នៅពេលបញ្ជាផ្សិតចិញ្ចៀន សមាមាត្របង្ហាប់នៃរន្ធបីជួរនៅចុងទាំងពីរនៃទិសអ័ក្សនៃផ្សិតចិញ្ចៀនដើមអាចមានទំហំ 1-2mm តូចជាងនៅកណ្តាល។
(7) ប្រើកាំបិតកាត់ទន់ដែលមានកម្រាស់គ្រប់គ្រងចន្លោះពី 0.5-1mm ដើម្បីធានាបាននូវគែមមុតស្រួចតាមដែលអាចធ្វើទៅបាន ដើម្បីឱ្យវាស្ថិតនៅលើបន្ទាត់សំណាញ់រវាងផ្សិតសង្វៀន និងឧបករណ៍រំកិលសម្ពាធ។
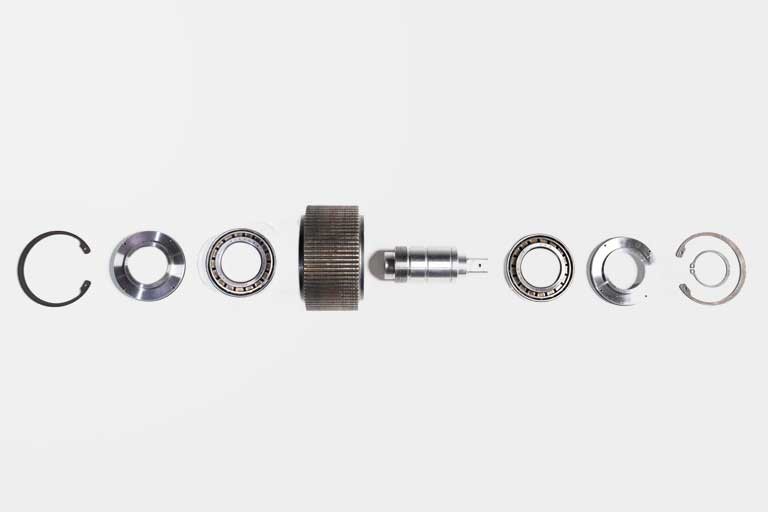
(8) ធានាបាននូវភាពច្របូកច្របល់នៃផ្សិតចិញ្ចៀន ពិនិត្យជាទៀងទាត់នូវការបោសសំអាត spindle នៃ granulator និងកែតម្រូវវាប្រសិនបើចាំបាច់។
៦. ចំណុចត្រួតពិនិត្យសង្ខេប៖
1. ការកិន: ភាពល្អិតល្អន់នៃការកិនត្រូវតែត្រូវបានគ្រប់គ្រងដោយយោងទៅតាមតម្រូវការជាក់លាក់
2. ការលាយបញ្ចូលគ្នា៖ ឯកសណ្ឋាននៃការលាយវត្ថុធាតុដើមត្រូវតែត្រូវបានគ្រប់គ្រង ដើម្បីធានាបាននូវបរិមាណលាយសមស្រប ពេលវេលាលាយ សំណើម និងសីតុណ្ហភាព។
3. ភាពចាស់ទុំ៖ សម្ពាធ សីតុណ្ហភាព និងសំណើមរបស់ម៉ាស៊ីនផ្លុំត្រូវតែគ្រប់គ្រង
ទំហំ និងរូបរាងរបស់សម្ភារៈភាគល្អិត៖ លក្ខណៈបច្ចេកទេសសមស្របនៃផ្សិតបង្ហាប់ និងកាំបិតកាត់ត្រូវតែត្រូវបានជ្រើសរើស។
5. មាតិកាទឹកនៃចំណីដែលបានបញ្ចប់: វាចាំបាច់ដើម្បីធានាបាននូវពេលវេលាស្ងួតនិងត្រជាក់និងសីតុណ្ហភាព។
6. ការបាញ់ថ្នាំប្រេង៖ ចាំបាច់ត្រូវគ្រប់គ្រងបរិមាណជាក់លាក់នៃការបាញ់ប្រេង ចំនួនក្បាលបូម និងគុណភាពនៃប្រេង។
7. ការបញ្ចាំង: ជ្រើសរើសទំហំនៃ Sieve បានដោយយោងទៅតាមលក្ខណៈបច្ចេកទេសនៃសម្ភារៈ។
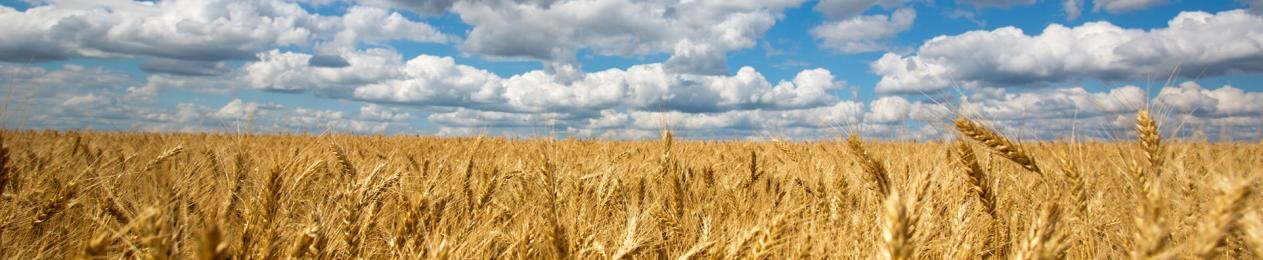
ពេលវេលាបង្ហោះ៖ ថ្ងៃទី ៣០ ខែវិច្ឆិកា ឆ្នាំ ២០២៣